L-Valine Production Solution
L-Valine is an essential amino acid widely used in the pharmaceutical, food additive, and feed industries. Its production process primarily consists of four main stages: the pretreatment stage, the fermentation stage, the extraction stage, and the refinement stage. Each stage has its specific process objectives and operational requirements, and by strictly controlling process parameters, a high-purity valine product is ultimately produced.
We provide a full range of engineering services, including project preparatory work, overall design, equipment supply, electrical automation, installation guidance and commissioning.
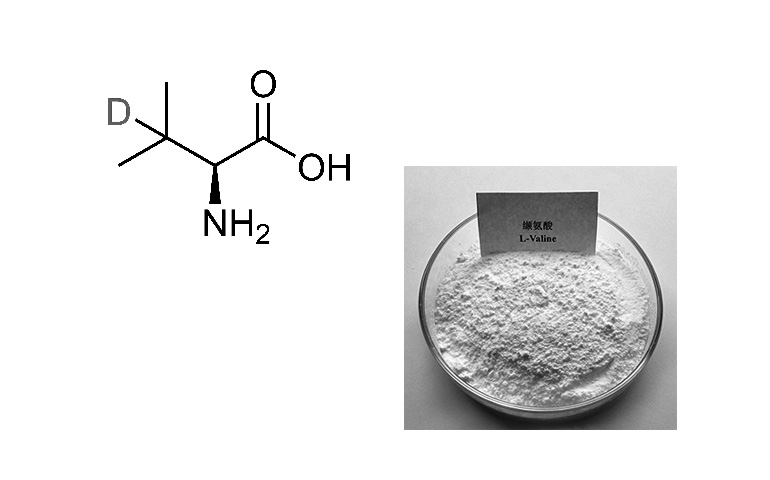
Process Flow of L-Valine Production
Glucose
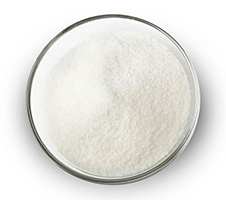
L-Valine
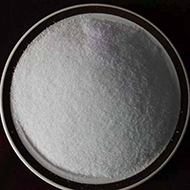
COFCO Technology & Industry Technical Advantages
I. Advanced Fermentation Technology
1. Efficient Strain Selection and Breeding
Genetic Engineering Technology: COFCO Tech utilizes gene editing technologies (e.g., CRISPR-Cas9) to optimize production strains, developing high-yield valine-producing strains (such as Corynebacterium glutamicum or Escherichia coli).
Metabolic Engineering: By regulating the metabolic pathways of the strains, the synthesis efficiency of valine is improved, and the generation of byproducts is reduced.
Strain Stability: The selected strains exhibit high genetic stability and stress resistance, making them suitable for large-scale industrial production.
2. Process Optimization
High-Density Fermentation: High-density fermentation technology is employed to increase bacterial concentration and valine yield.
Fed-Batch Strategy: Through fed-batch techniques, the addition of carbon sources, nitrogen sources, and trace elements is precisely controlled to avoid substrate inhibition and enhance production efficiency.
Process Control: Advanced online monitoring systems (e.g., pH, dissolved oxygen, and temperature sensors) are used to regulate fermentation conditions in real time, ensuring the efficiency and stability of the fermentation process.
II. Green Production Process
1. Clean Production Technology
Energy Saving and Emission Reduction: Energy consumption and wastewater discharge are reduced by optimizing fermentation processes and equipment.
Waste Resource Utilization: Bacterial residues and waste liquid generated during fermentation are repurposed, such as being converted into organic fertilizers or feed additives.
2. Environmentally Friendly Extraction Technology Membrane Separation Technology: Ultrafiltration and nanofiltration are used to replace traditional chemical extraction methods, reducing the use of organic solvents.
Ion-Exchange Technology: High-efficiency ion-exchange resins are utilized to improve the extraction rate and purity of valine while minimizing wastewater discharge.
III. Intelligent and Automated Production
1. Smart Manufacturing
Automation Control System: Distributed Control Systems (DCS) and Programmable Logic Controllers (PLC) are adopted to achieve automated control of the production process.
Big Data and Artificial Intelligence: Big data analytics and AI technologies are used to optimize production process parameters, enhancing production efficiency and product quality.
2. Full-Process Traceability System
Quality Traceability: A comprehensive traceability system is established, covering raw materials to finished products, ensuring product quality control and traceability.
Real-Time Monitoring: IoT technology enables real-time monitoring of key parameters during production, allowing- Real-Time Monitoring: IoT technology enables real-time monitoring of key parameters during production, allowing for timely detection and resolution of issues.
IV. R&D and Innovation Capabilities
1. Strong R&D Team
Research Talent: The company boasts a high-caliber R&D team, covering multiple fields such as microbiology, bioengineering, and chemical engineering.
R&D Investment: Significant annual investments are made in technological research and innovation to maintain a leading position in the industry.
2. Industry-Academia-Research Collaboration
University Partnerships: Collaborations with renowned domestic and international universities and research institutions are established to conduct cutting-edge technology research.
Technology Transfer: Research outcomes are rapidly translated into practical production capabilities, driving technological advancement and industrial upgrading.
1. Efficient Strain Selection and Breeding
Genetic Engineering Technology: COFCO Tech utilizes gene editing technologies (e.g., CRISPR-Cas9) to optimize production strains, developing high-yield valine-producing strains (such as Corynebacterium glutamicum or Escherichia coli).
Metabolic Engineering: By regulating the metabolic pathways of the strains, the synthesis efficiency of valine is improved, and the generation of byproducts is reduced.
Strain Stability: The selected strains exhibit high genetic stability and stress resistance, making them suitable for large-scale industrial production.
2. Process Optimization
High-Density Fermentation: High-density fermentation technology is employed to increase bacterial concentration and valine yield.
Fed-Batch Strategy: Through fed-batch techniques, the addition of carbon sources, nitrogen sources, and trace elements is precisely controlled to avoid substrate inhibition and enhance production efficiency.
Process Control: Advanced online monitoring systems (e.g., pH, dissolved oxygen, and temperature sensors) are used to regulate fermentation conditions in real time, ensuring the efficiency and stability of the fermentation process.
II. Green Production Process
1. Clean Production Technology
Energy Saving and Emission Reduction: Energy consumption and wastewater discharge are reduced by optimizing fermentation processes and equipment.
Waste Resource Utilization: Bacterial residues and waste liquid generated during fermentation are repurposed, such as being converted into organic fertilizers or feed additives.
2. Environmentally Friendly Extraction Technology Membrane Separation Technology: Ultrafiltration and nanofiltration are used to replace traditional chemical extraction methods, reducing the use of organic solvents.
Ion-Exchange Technology: High-efficiency ion-exchange resins are utilized to improve the extraction rate and purity of valine while minimizing wastewater discharge.
III. Intelligent and Automated Production
1. Smart Manufacturing
Automation Control System: Distributed Control Systems (DCS) and Programmable Logic Controllers (PLC) are adopted to achieve automated control of the production process.
Big Data and Artificial Intelligence: Big data analytics and AI technologies are used to optimize production process parameters, enhancing production efficiency and product quality.
2. Full-Process Traceability System
Quality Traceability: A comprehensive traceability system is established, covering raw materials to finished products, ensuring product quality control and traceability.
Real-Time Monitoring: IoT technology enables real-time monitoring of key parameters during production, allowing- Real-Time Monitoring: IoT technology enables real-time monitoring of key parameters during production, allowing for timely detection and resolution of issues.
IV. R&D and Innovation Capabilities
1. Strong R&D Team
Research Talent: The company boasts a high-caliber R&D team, covering multiple fields such as microbiology, bioengineering, and chemical engineering.
R&D Investment: Significant annual investments are made in technological research and innovation to maintain a leading position in the industry.
2. Industry-Academia-Research Collaboration
University Partnerships: Collaborations with renowned domestic and international universities and research institutions are established to conduct cutting-edge technology research.
Technology Transfer: Research outcomes are rapidly translated into practical production capabilities, driving technological advancement and industrial upgrading.
Lysine Production Projects
Related Products
You Are Welcome To Consult Our Solutions, We Will Communicate With You In Time And Provide
Professional Solutions
Full Lifecycle Service
We provide customers with full life cycle engineering services such as consulting, engineering design, equipment supply, engineering operation management, and post renovation services.
We're Here to Help.
Frequently Asked Questions
-
CIP Cleaning System+CIP cleaning system device is a non-decomposable production equipment and a simple and safe automatic cleaning system. It is used in almost all food, beverage and pharmaceutical factories.
-
A Guide to Pressed and Extracted Oils+There are significant differences between the pressed oil and extracted oil in terms of processing techniques, nutritional content, and raw material requirements.
-
Scope of Technical Service for Grain-based Biochemical Solution+At the core of our operations are internationally advanced strains, processes, and production technologies.
Inquiry