L-Arginine Production Solution
Arginine (L-arginine) is a basic amino acid with important physiological functions, and modern industrial production primarily relies on microbial fermentation methods. This process uses glucose as the main carbon source, employing genetically engineered Corynebacterium glutamicum or Escherichia coli for efficient biosynthesis, followed by multi-stage separation and purification to obtain the final product.
We provide a full range of engineering services, including project preparatory work, overall design, equipment supply, electrical automation, installation guidance and commissioning.
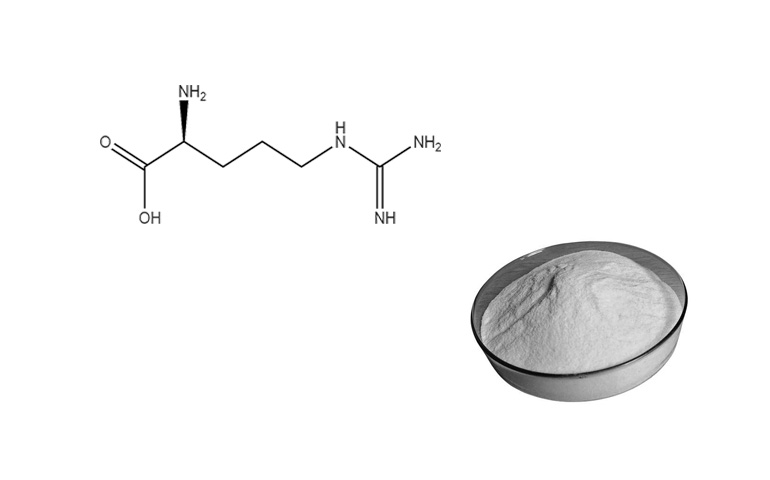
Process Flow of Microbial Fermentation Method
Glucose
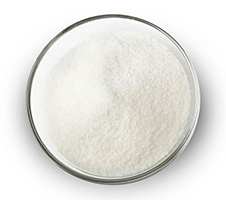
L-Arginine
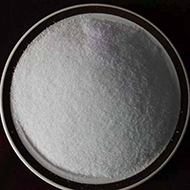
COFCO Technology & Industry Technical Advantages
I. New Fermentation Process
1. Continuous Fermentation Technology: Compared to traditional batch fermentation, the multi-stage continuous fermentation system can increase equipment utilization by 30% and reduce energy consumption by 15%.
2. Mixed Carbon Source Utilization: Using a combination of corn starch and molasses for fermentation ensures bacterial growth rates while reducing raw material costs (a 20% cost reduction compared to pure starch fermentation).
II. Efficient Separation and Purification Technology System
1. Application of Membrane Integration Technology
Combined with continuous ion-exchange chromatography, this enables efficient separation of the target product.
2. Optimized Crystallization Process
Multi-Stage Gradient Crystallization Control: Using a water-ethanol system, high-uniformity crystals (bulk density ≥ 0.7 g/cm³) are obtained by precisely controlling the cooling rate and solvent ratio, significantly improving product flowability and reducing agglomeration.
Mother Liquor Recycling: After desalination, the crystallization mother liquor is reused in the fermentation stage, increasing the overall raw material utilization rate to over 98%.
III. Green Manufacturing & Cost Control
1. Energy Conservation & Emission Reduction Technologies
Wastewater Treatment: Fermentation effluent is treated via anaerobic-aerobic coupled processes, achieving >90% COD removal. Recovered biogas is utilized for boiler heating (annual CO₂ reduction: ~12,000 tons).
Heat Recovery: Waste heat from fermentation tank sterilization steam preheats culture media, reducing steam consumption by 25%.
2. Raw Material Localization & Substitution
Non-Grain Carbon Source Application: Pilot trials using cassava and straw hydrolysate to replace corn starch in select production lines, reducing reliance on food-grade feedstocks (15% cost reduction in pilot phase).
IV. R&D & Industrial Chain Synergy
1. Industry-Academia-Research Collaboration
Jointly established the Amino Acid Manufacturing Joint Laboratory with Jiangnan University and Tianjin Institute of Industrial Biotechnology, focusing on strain iteration and process scale-up.
2. Industrial Chain Extension
High-Value Byproduct Utilization: Fermentation residues are converted into organic fertilizers or feed proteins.
Downstream Application Development: Proprietary derivatives (e.g., arginine hydrochloride, arginine glutamate) developed to expand into pharmaceutical intermediate markets.
1. Continuous Fermentation Technology: Compared to traditional batch fermentation, the multi-stage continuous fermentation system can increase equipment utilization by 30% and reduce energy consumption by 15%.
2. Mixed Carbon Source Utilization: Using a combination of corn starch and molasses for fermentation ensures bacterial growth rates while reducing raw material costs (a 20% cost reduction compared to pure starch fermentation).
II. Efficient Separation and Purification Technology System
1. Application of Membrane Integration Technology
Combined with continuous ion-exchange chromatography, this enables efficient separation of the target product.
2. Optimized Crystallization Process
Multi-Stage Gradient Crystallization Control: Using a water-ethanol system, high-uniformity crystals (bulk density ≥ 0.7 g/cm³) are obtained by precisely controlling the cooling rate and solvent ratio, significantly improving product flowability and reducing agglomeration.
Mother Liquor Recycling: After desalination, the crystallization mother liquor is reused in the fermentation stage, increasing the overall raw material utilization rate to over 98%.
III. Green Manufacturing & Cost Control
1. Energy Conservation & Emission Reduction Technologies
Wastewater Treatment: Fermentation effluent is treated via anaerobic-aerobic coupled processes, achieving >90% COD removal. Recovered biogas is utilized for boiler heating (annual CO₂ reduction: ~12,000 tons).
Heat Recovery: Waste heat from fermentation tank sterilization steam preheats culture media, reducing steam consumption by 25%.
2. Raw Material Localization & Substitution
Non-Grain Carbon Source Application: Pilot trials using cassava and straw hydrolysate to replace corn starch in select production lines, reducing reliance on food-grade feedstocks (15% cost reduction in pilot phase).
IV. R&D & Industrial Chain Synergy
1. Industry-Academia-Research Collaboration
Jointly established the Amino Acid Manufacturing Joint Laboratory with Jiangnan University and Tianjin Institute of Industrial Biotechnology, focusing on strain iteration and process scale-up.
2. Industrial Chain Extension
High-Value Byproduct Utilization: Fermentation residues are converted into organic fertilizers or feed proteins.
Downstream Application Development: Proprietary derivatives (e.g., arginine hydrochloride, arginine glutamate) developed to expand into pharmaceutical intermediate markets.
Lysine Production Projects
Related Products
You Are Welcome To Consult Our Solutions, We Will Communicate With You In Time And Provide
Professional Solutions
Full Lifecycle Service
We provide customers with full life cycle engineering services such as consulting, engineering design, equipment supply, engineering operation management, and post renovation services.
We're Here to Help.
Frequently Asked Questions
-
CIP Cleaning System+CIP cleaning system device is a non-decomposable production equipment and a simple and safe automatic cleaning system. It is used in almost all food, beverage and pharmaceutical factories.
-
A Guide to Pressed and Extracted Oils+There are significant differences between the pressed oil and extracted oil in terms of processing techniques, nutritional content, and raw material requirements.
-
Scope of Technical Service for Grain-based Biochemical Solution+At the core of our operations are internationally advanced strains, processes, and production technologies.
Inquiry